Valcorp Enterprises has been in business since 2015 serving the Department of Defense (DOD) and bases in and around Texas. Valcorp had become known to the DLA (Defense Logistics Agency) as a “solutions provider” taking on jobs, many that are too complex for others. The team’s experience with dealing with government agencies and extensive knowledge of the regulations enabled them to take on work no one else wanted. In 2019 Valcorp decided to expand their capabilities to fill a void they noticed with the DLA and expanded their capabilities by providing fabricated and machined parts.
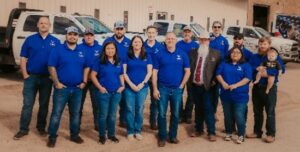
The Situation
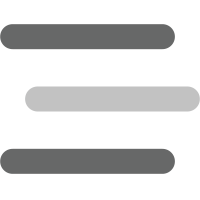
During Valcorp Enterprise’s first year of manufacturing operations their customers were strictly DOD and the Defense Logistics Agency (DLA) Troop Support and Land and Maritime. The DLA is the nation’s combat logistics support agency and their manufacturing was performed through contract manufacturers. After a year into fabrication and manufacturing, to further their capabilities and gain control of the manufacturing Valcorp purchased equipment to open their own manufacturing facility in Haltom City, seeing this diversification as another way to support the war fighter. Although FAR 46.105 detailed that that the supplier must carry out contractual QA obligations, in 2019 the DLA released requirements detailing that contracts with higher-level quality requirements be required for suppliers to establish and maintain a documented QMS
While reaching out to win new work in the local commercial aerospace and defense sector Valcorp realized they were challenged by the lack of AS9100 certification. The organization was missing out on critical contract opportunities with commercial aerospace and defense companies and was having difficulty diversifying their customer base and attracting new businesses without certification. Prospective customers were specifically citing the absence of AS9100 certification as an issue because their supply chain procedures stipulated suppliers have an ISO certification.
The Solution
In March 2021 Valcorp reached out to have TMAC lead them through the process of developing and implementing a Quality Management System that met the requirements of AS9100 while fitting the scope and complexity of their small, growing manufacturing shop.
WORKING THROUGH THE IMPLEMENTATION
TMAC worked with Valcorp Enterprises personnel through the following (4) phases of QMS implementation between March and December 2021:
- Commitment and Organizational Context – working closely with leadership to define the scope, organizational structure, interested parties, interactions, Quality Policy and a communication plan
- Identification of risks and opportunities, statutory and regulatory impacts, and organizational objectives
- Development of Management System Documentation with input from personnel at all levels
- Evaluation (Internal Audit) of the Quality System and execution of corrective actions to close identified gaps
The AS9100 D external audit was performed by the registrar in January 2022 and after successfully completing and submitted information into OASIS for several minor nonconformances Valcorp was awarded their AS9100 D certification on February 24, 2022.
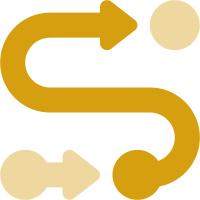
The Results
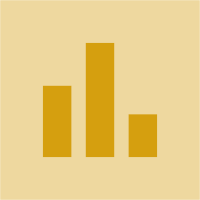
Since beginning their work with TMAC on their AS9100D certification, Valcorp has:
- Moved into a larger facility
- Invested in new equipment (new 5-Axis CNC)
- Created and hired six new employees
- Retained sales from current customers
- Due to improved quality and OTD expecting over a 400% increase in sales
- Received recognition from DLA for “appreciated your creative problem solving”
Valcorp commented that they were excited to continue to work with TMAC to continually improve their QMS and grow their team to fulfill their vision to be nationally recognized as a solutions provider of exceptional quality solutions for the military and defense.
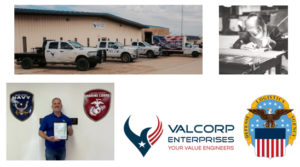
TMAC at UTA allowed us to on-board quality expertise quickly and provided us the guidance to implement a right-sized solution for our organization’s Quality System, getting us from zero to 100% in less than a year.
Jason Petras
Vice President