Creative Foodworks is a food manufacturing company located in San Antonio, Texas that manufactures and packages foods to be sold by a wide variety of customers throughout the United States. Using ingredients specified by their customer, they mix (batch), cook, bottle, and package food products in a range of bottle sizes and volumes.
Creative Foodworks was established in 1994 and after 25 successful years, the owners decided to retire. In 2021, new owners acquired the company. The new owners recognized the potential for significant growth and efficiency gains.
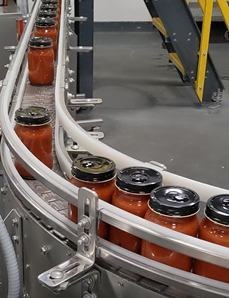
The Situation
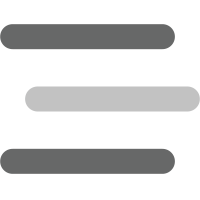
Creative Foodworks was recently acquired by new ownership. Taking over a company is no easy feat. It requires unquestionable determination and a fierce commitment. Seeing the potential for efficiency gains and growth, Creative Foodworks reached out to TMAC for assistance with two specific goals. The first goal was to capture tribal knowledge to ensure continued effectiveness of key processes once the prior owners transitioned out of the company. “Tribal knowledge” is a term that refers to any information that is not widely known by other employees within a company. It is not documented and exists only in the minds of certain people. The second goal was to have a comprehensive understanding of the existing production capacity to determine bottlenecks and to evaluate the impact of integrating additional equipment into the production line.
The Solution
Since tribal knowledge is a barrier to sustainable, long-term growth, capturing it before the prior owners transitioned out of the company was a high priority. TMAC observed the identified key processes and documented standard operating procedures (SOPs) for these crucial administrative tasks. The SOPs included more than the simple step-by-step instructions. They also included the knowledge, tips, and tricks about the tasks that no one else had access to. These SOPs were then used to train a new employee to continue with the efficiency and effectiveness required to maintain business operations.
TMAC also conducted a capacity assessment that involved the collection and analysis of field data that served as real-life inputs to a computer simulation of the production process. From there, TMAC ran multiple scenarios to isolate the root cause of production bottlenecks when operating at elevated capacities. The output from the simulation provided a framework for increased production capacity, which aided in the growth of the company.
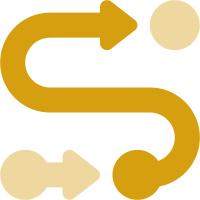
The Results
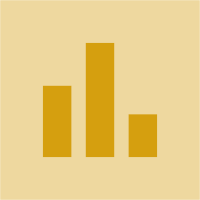
As Creative Foodworks continues to grow, they now have data to ensure success. The SOPS have allowed current manufacturing obligations to be met because processes were maintained. Over time, these SOPs have been updated to account for improvements the new owners have implemented. Furthermore, Creative Foodworks now has a complete understanding of the capacity of each component on the production line. With this knowledge, they informed decisions were made on the appropriate components and required capabilities to add to the line to increase production capacity by over 15%.
- Increased production capacity by 15%
- Documented Standard Operating Procedures (SOPs)
- Capacity Assessment
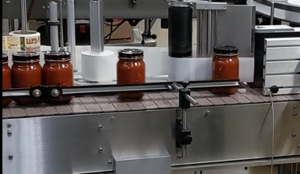
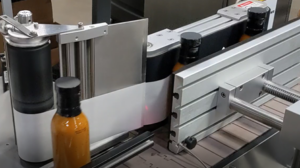
By knowing current capacity and understanding what is required to add capacity, we have been able to reduce costs while significantly growing the business.
Troy Riegel
President & CEO