With our lean manufacturing services, manufacturers can effectively reduce waste caused by long lead times, complex changeovers, and productivity losses. Our team of experts are deeply committed to helping Texas manufacturers overcome challenges that hinder their progress, reaching important project milestones, and accelerate their profitable growth.
We take pride in our approach of assisting manufacturers in waste elimination through continuous process improvement. Our strategy entails crafting a customized lean implementation action plan. Through our hands-on approach, we guarantee success in implementing new processes, resulting in increased efficiency and smoother operations.
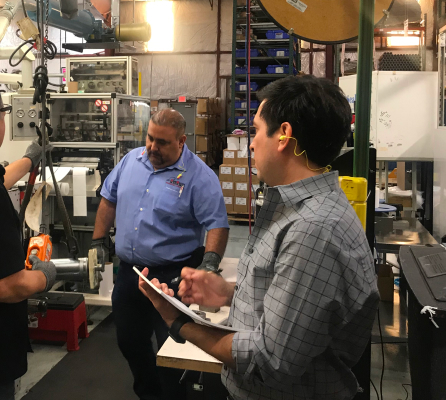
Some Lean Manufacturing Services we offer
Lean Six Sigma
Lean Six Sigma is a structured, data-based approach to solve business problems. It is a powerful methodology to implement a successful Operational Excellence Program and to help achieve strategic objectives.
LSS empowers employees with new skills, turning them into Leaders now and into the future.
Value Stream Mapping
TMAC works with manufacturers in documenting and analyzing the flow of information and/or materials, optimizing efficiency to eliminate waste and decrease production costs.
Toyota Kata
Toyota Kata is a management methodology derived from the practices of Toyota Production System (TPS) and is focused on achieving continuous improvement and problem-solving capabilities within organizations. It consists of two primary routines: Improvement Kata and Coaching Kata.
- Improvement Kata involves setting ambitious goals, breaking them down into smaller, achievable steps, experimenting, and learning through iterative cycles.
- Coaching Kata emphasizes the role of leaders in guiding employees through the Improvement Kata process, fostering a culture of coaching, mentorship, and development.
By embracing Toyota Kata, organizations can cultivate a mindset of continuous learning, adaptability, and innovation, enabling them to effectively navigate challenges and achieve their strategic objectives.
5S
5S is a systematic methodology used to organize and maintain workplace efficiency through five key principles: Sort, Set in Order, Shine, Standardize, and Sustain.
The approach aims to create a clean, orderly, and standardized work environment that fosters productivity, safety, and quality. By sorting through items, organizing workspaces, maintaining cleanliness, establishing standards, and ensuring ongoing adherence, 5S facilitates continuous improvement and employee engagement.
Implemented across various industries, 5S not only enhances operational efficiency but also promotes a culture of discipline, teamwork, and excellence within organizations.
Total Productive Maintenance
Late deliveries, extended lead times, and customer dissatisfaction often stem from machine breakdowns. The Texas Manufacturing Assistance Center offers a solution to mitigate these issues through total productive maintenance (TPM) strategy.
Implementing a TPM strategy enables organizations to enhance the availability, performance efficiency, and quality of their production machines.