At the forefront of Impact Recovery Systems, Inc.® is the mission to provide quality safety products to its customers. Since 1991, they have manufactured flexible, high-impact traffic and safety devices for roads, pedestrian safety, warehouses, and facilities worldwide.
Utilizing Robots and Process Improvement Techniques to Improve Turnaround Time
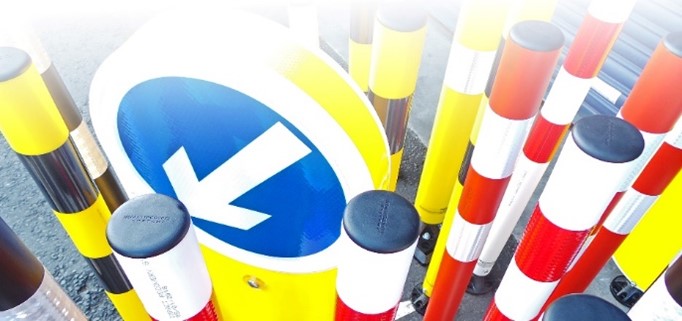
The Situation
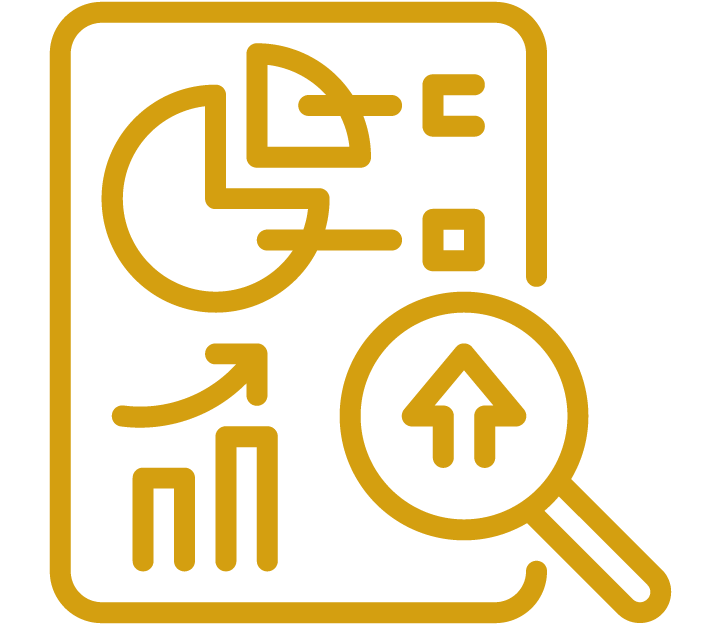
President Greg Hannah says, “It has always been the goal of Impact Recovery Systems, Inc.® to be the premier manufacturer of safety products. From early on, we knew that to do so, we would have to continuously review our manufacturing processes. As Impact Recovery Systems, Inc.® has grown, added new products, and people, it is imperative that we continue to focus on quality, cost, and delivery to allow more flexibility and responsiveness for our customers.”In 2007, Impact Recovery Systems, Inc.® first engaged with TMAC at Southwest Research Institute (SwRI). Over the years, Impact Recovery Systems, Inc.® has worked closely with TMAC, in what has now become a culture of continuous improvement. Together, TMAC and Impact Recovery Systems, Inc.® have implemented continuous flow, moved to a new facility, expanded their new facility and deployed a Quality Management System. Production/Purchasing/Inventory Manager Barbara Cheatham shares, “TMAC has always fulfilled our needs when we have leveraged their help. Their team is very knowledgeable and has vast experience in helping manufacturers become better.” Cheatham is one of the main forces leading the charge. With more than 37 years of manufacturing experience, she knows the importance of continuous improvement. Specifically, she says, “Process improvement helps with inventory, which in turn will help with purchasing, scheduling, quality, and customer satisfaction. From the office to the shop floor, process improvement can benefit any company by decreasing costs, shortening lead times, reducing defects, and minimizing inventory. This results in increased capacity, improved customer satisfaction, and higher profits.” In 2021, Impact Recovery Systems, Inc.® was experiencing rapid growth and was feeling the growing pains. Without hesitation they reached out to TMAC for assistance in automating processes and for improving production flow based on new processes and product mix.
The Solution
Part one of the solution involved automating a key process step. Dexterous handling of components during a plastic spin welding process created an obstacle for affordable automation integration. Plant engineers wanted to know if it was possible to utilize a robotic pick and place solution for the spin welding process that could also co-exist with human operators on a busy factory floor. TMAC re-created the spin welding work cell at TMAC’s Collaborative Robotic Facility with the intent of showing how a collaborative robot, a system that may be safely used around humans with a semi-custom end of arm tool, can reliably assemble components for spin welding process. TMAC engineers were able to demonstrate the collaborative robotic pick and place solution in various configurations that completed the pick and place process within the required process time. In parallel, TMAC analyzed the company’s products, processes, technologies, and people. One of the key tools involved was Value Stream Mapping, which allowed the Impact Recovery Systems, Inc.® team to clearly analyze their current process and identify opportunities. Once the key opportunities were identified, the team utilized tools such as Cellular Manufacturing, Total Productive Maintenance, and 5S (workplace organization) to further delve into areas of improvement. TMAC professional, Sandra Hawkins, explains, “With growth, the biggest area of improvement is processing the increased number of orders quickly. To achieve this, Impact Recovery Systems, Inc.® has identified the need to modify their facility layout to increase flow and create a pull system.” However, process improvement alone cannot guarantee a company’s success. The culture of the company (from its leadership to the workers), must be one of growth and progress. Every employee must believe that what they do is important and plays an important role in the success of the company. They must also be encouraged to take ownership by speaking up about broken processes or finding solutions to existing challenges. At Impact Recovery Systems, Inc.® the leadership team involves employees in process improvement initiatives, as well as rewards employees who engage in process improvement. As Cheatham concludes, “It’s great that our leadership is committed to investing in the business to help it grow and thrive.” By incorporating process improvement practices into its daily manufacturing practices, the culture of continuous improvement will become second nature at Impact Recovery Systems, Inc.®
The Result
As Impact Recovery Systems continues to grow, they now have the confirmation that an automated spin weld process will improve throughput by more than 20% and will yield a more consistent product. With the implementation of Flow Manufacturing, work in process inventory was reduced by 40%, which significantly improved turnaround time. Customer satisfaction has improved while costs were reduced through improved quality and elimination of non‐productive time by rearranging equipment and personnel.
20% improved throughput
Yield a more consistent product
Work in Process reduced by 40%
improved turnaround time
Improved customer satisfaction
Next Steps
TMAC has always fulfilled our needs when we have leveraged their help. Their team is very knowledgeable and has vast experience in helping manufacturers become better.
- Barbara Cheatham
Production/Purchasing/Inventory Manager