E3: Economy-Environmental-Energy Assessments conducted with five Food & Beverage Manufacturers revealed many common opportunities to reduce costs and wastes…all impacting the bottom line. Funded by a pollution prevention grant, TMAC reached out to organizations in both Texas and Louisiana to participate in an E3 Assessment. Participants ranged from a small specialty chocolate maker to a major coffee producer. Each highly unique, but each shared some common opportunities for continual improvement.
E3: Economy-Environmental-Energy Assessments
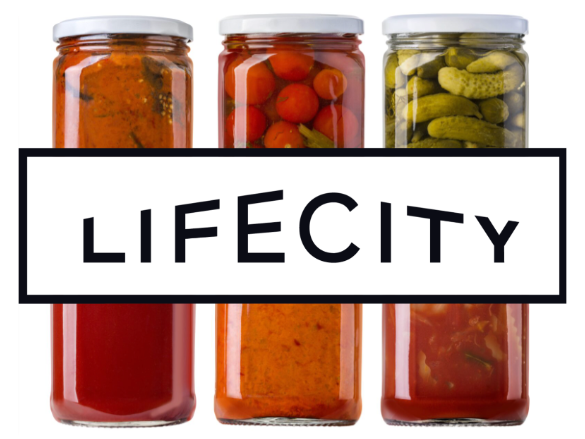
The Situation
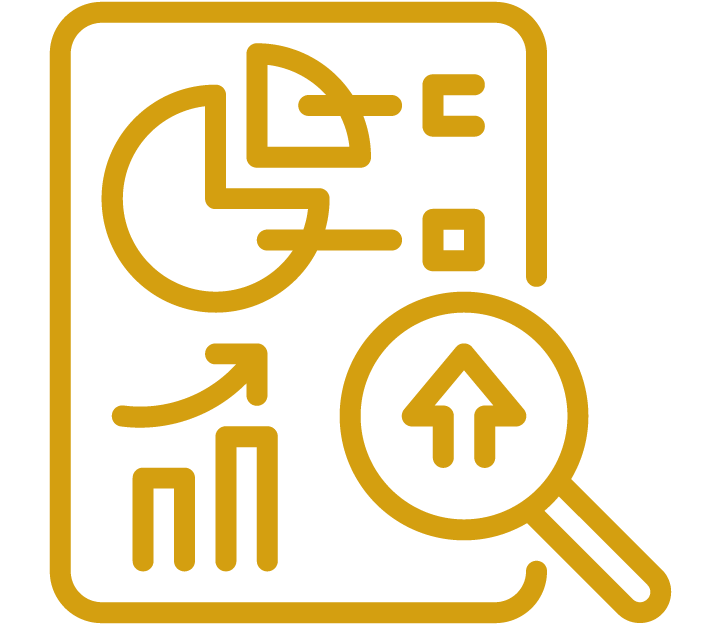
TMAC needed to locate Food & Beverage Manufacturers that were interested in receiving assistance that would be fully funded by a pollution prevention grant. TMAC partnered with the Texas Food Processor Association (TFPA) to learn more about food manufacturing across the state. TMAC also partnered with LifeCity, an impact management firm, that helps define, measure, validate, and market impact for organizations seeking sustainable solutions.
The Solution
The E3 delivery provided the manufacturers with customized, hands-on assessments of production processes to reduce costs and energy consumption, prevent pollution, increase productivity, and drive innovation. Working with a team from each organization the two day onsite effort guided the group through class room discussion followed by walking the production floor to identify waste opportunities. Each organization had unique processes to make their product, but many of the same opportunities for improvement were found across these five assessments. The first common issue included the Lean waste of transportation, specifically walking. The teams observed operators walking long distances to reach ingredients that needed to be weighed to create batches of products. Because multiple batches were mixed daily, this non-value-added time became a significant opportunity to reduce labor time necessary to complete this task. The next common observation included automated machines that were producing defects. The teams observed that operators were typically placed by the machine to correct the defects rather than address the root cause of the automation issue. Another common issue observed by the teams was understanding how long change overs can slow their ability to produce the products they need. Many of the changeover times were taking 45 minutes or longer. Common energy wastes included compressed air leaks and inappropriate uses of compressed air to remove moisture or move products. Opportunities to reduce water usage included replacing high flow spray nozzles with low volume high pressure nozzles for cleaning operations. Replacing out dated lighting with LED technology was a consistent action to reduce energy costs by all the facilities.
The Result
The 5 Food & Beverage manufacturers reported the following impact as a result of the E3 assessments:
7 MILLION
dollars of cost savings318,000
gallons of water reductions2,300,000 KWH
electrical reductions287 TON
reduction of solid wastesNext Steps
This assessment has been very beneficial to validate concerns we have had for years. We were reminded of things that we have been overlooking that need to be addressed. We now have a process to teach our supervisors how to identify and assign corrective actions to address these opportunities for improvement.
- Manufacturing Supervisor