NPIC is an industry leader in pet treats and understands that PETS ARE FAMILY. Since 1996, NPIC has been manufacturing high-quality, nutritious, and functional products to ensure the wellness, happiness, and longevity of all pets. They accomplish this through ongoing INNOVATION in all aspects of their business, from product development, to consumer education, to ensuring the continued growth and enrichment of their employees.
Begging for Innovated Improvements
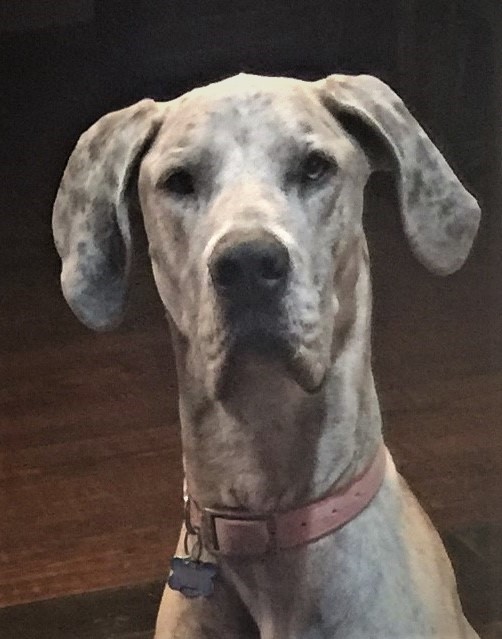
The Situation
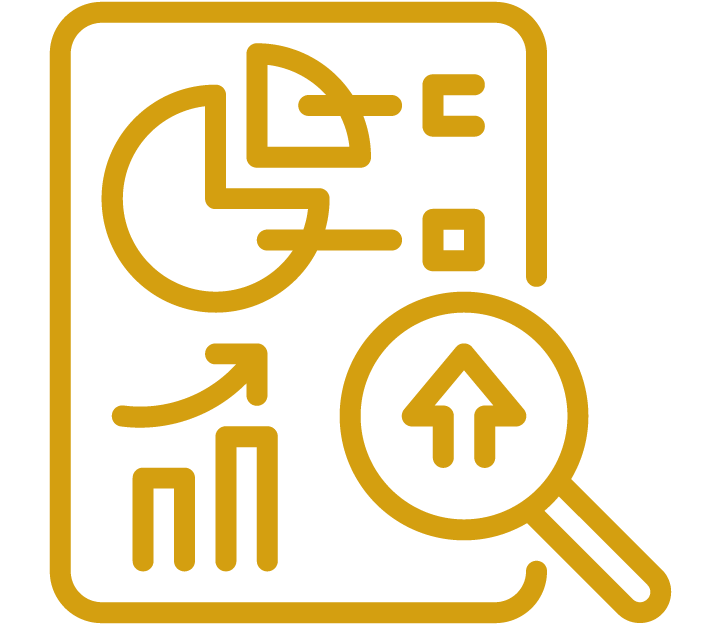
As part of a pollution prevention grant providing onsite assistance to Food & Beverage manufacturers, TMAC reached out to NPIC to see if they were interested in receiving assistance to provide training to their staff on how to identify opportunities to reduce waste throughout their facility.
The Solution
TMAC staff met with NPIC Executive Vice President, Josh Liu and toured their Plano, Texas location to gain a better understanding of their operations. TMAC returned and provided 3 days of onsite training working with a cross-functional team from NPIC. The team was introduced to the concepts of Lean Manufacturing and spent some time talking about adding value for their customer. Once the classroom training was completed, the team then walked the production floor to practice how to identify possible improvement opportunities. The team also took videos of several operations that were performing non-value-added tasks. The videos were then reviewed step by step and were documented in a simple Excel form to help the team to better analyze and question each movement. Once the lean opportunities were recorded the team then walked through some calculations to determine estimated savings for each opportunity identified. The classroom training continued on day 2 with the introduction on how to identify and calculate savings and reductions by looking for energy and environmental opportunities. Once again the team returned to the production floor. The group quickly recognized that the hand washing sinks were using a large amount of water every time an employee washed their hands before entering their production floor. The team took several videos of the process and determined that each employee was using at least 20 ounces of water each time they washed their hands. Across all three shifts, this meant that they were using over 150 gallons a day. NPIC took action immediately and installed low flow nozzles to each of the 8 faucets which will now save over 30,000 of gallons of water each year. The spray nozzles not only reduce water use but they make it easier for employees to wash and rinse because of the spray’s larger coverage.
The Result
Next Steps
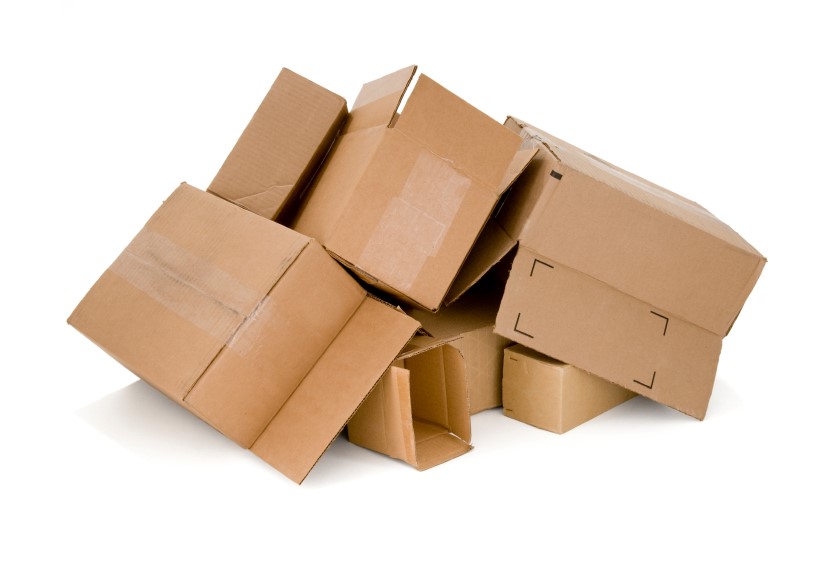
Next, the team observed an opportunity to separate cardboard from their solid waste collection. NPIC is now adding a cardboard compactor and bailer which will recycle 2.4 tons of cardboard and prevent future disposal of cardboard to the landfill.
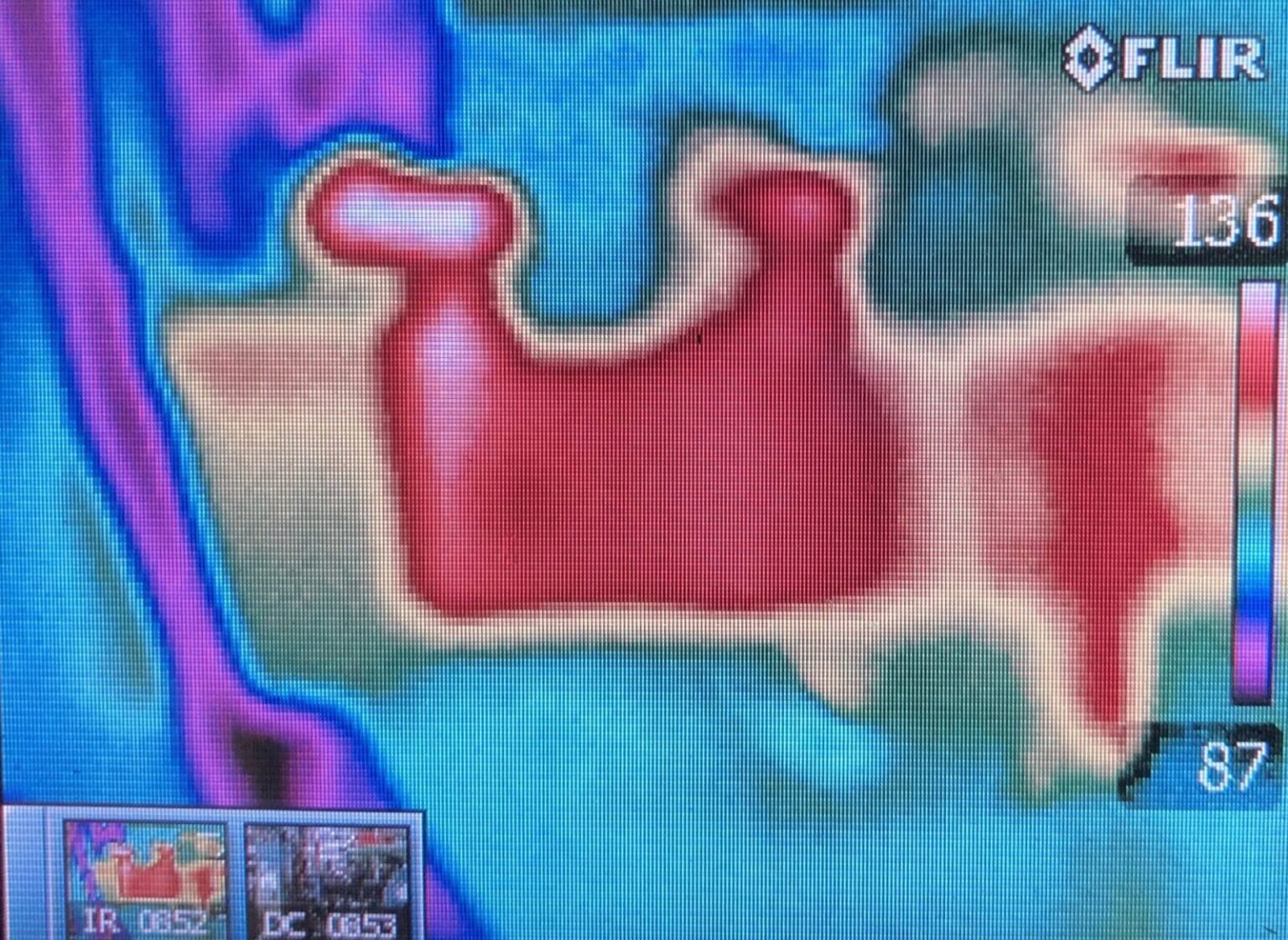
TMAC also used a thermal camera to help the team see how heat is escaping from their injection molding machines. NPIC is now working to install additional heat shielding around their heating coils to help reduce heat loss, save energy and maintain a consistent injection temperature to reduce rejects.
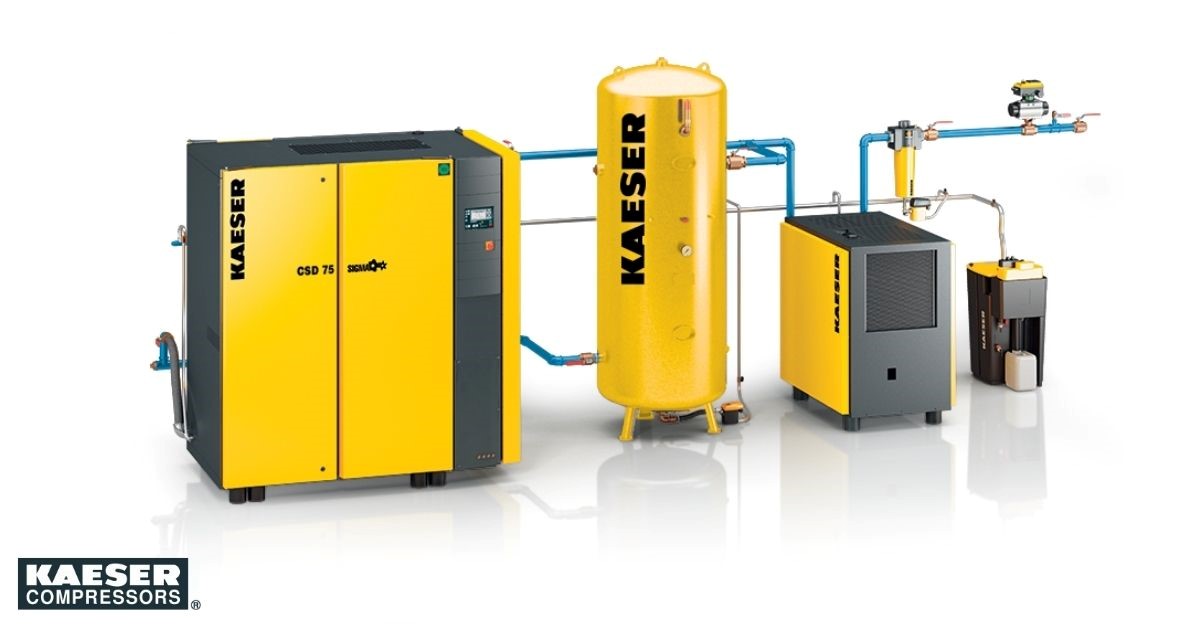
Finally, the team identified opportunities to reduce compressed air consumption by repairing leaks and adjusting compressor settings to better match the actual demands of their equipment. These improvements will reduce energy consumption by 69,000 kWh annually and will reduce energy costs by more than $5,800 annually.